Rapid Cold Welding Repair Technology of Electrochemical Catalytic Ionic Liquid Nickel Base Alloy
Disadvantages of welding repair (heat welding, cold welding)
Commonly used welding repair methods (electric welding, repair welding, surfacing, brazing, etc.) are all hot welding repair methods. The common problem with the hot-weld repair technology is that if post-weld treatment (such as heat treatment) is performed, a series of problems such as thermal stress deformation, cracking, and structural phase change of the repaired part cannot be eliminated.
In recent years, cold welding repair technology (supplement, fuse welding, laser cladding, etc.) can repair parts without increasing a high-temperature rise on the parts. Although these methods can reduce the adverse consequences of heat welding repair to a certain extent, there are other problems produced during these methods. For example, the patch method is not suitable for repairing metal materials with good electrical conductivity (such as copper, aluminum, and alloys thereof), fuse welding cannot eliminate pores, and laser cladding will reduce the fatigue resistance of shafts (such as crankshafts).
​
Rapid cold welding repair technology of electrochemical catalytic ionic liquid Nickel base alloy
Different from the welding repair (heat welding, cold welding) technology, the ionic liquid cold welding repair technology can rapidly and efficiently repair parts with a large-size difference under normal temperature conditions. More importantly, there is no quality hazard existing in the welding repair technology. The outstanding features of our cold welding technology include: 1) no heat impact (there is no thermal stress, thermal deformation, hot crack, and other defects after repairing the workpiece); 2) the repair thickness is large (up to 1mm or more); 3) the bonding strength is high (between the repair layer and the substrate For the metal key combination); 4) the repair speed is fast (20 wire left and right axis is out of tolerance, the repair time takes about 10 minutes); 5) the repair layer thickness is easy to control; 6) especially suitable for repairing deep holes of large basic components (such as engine Housing bearing hole and tile seat); 7) can be repaired online without subsequent processing; 8) can repair special-shaped parts which other maintenance methods cannot repair; 9) repair parts are not rust with good corrosion resistance; 10) easy to operate and low cost (for important parts, the cost of repair is minimum compared with its value).
​
Applications and practices
​​
-
Coal mine machinery
​
​
​
​
​
​
​
​
​
​
​
​
​
​
​
​
​
​
​
​
​
​
​
-
Rolling mill
​
​
​
​
​
​
​
​
​
​
​
​
​
​
​
​
​
​
​
​
​
​
​
-
Paper manufacturing machine
​
​
​
​
​
​
​
​
​
​
​
​
​
​
​
​
​
​
​
​
​
​
​
-
Wind power machinery
​
​
​
​
​
​
​
​
​
​
​
​
​
​
​
​
​
​
​
​
​
​
​
-
Copper foil machinery
​
​
​
​
​
​
​
​
​
​


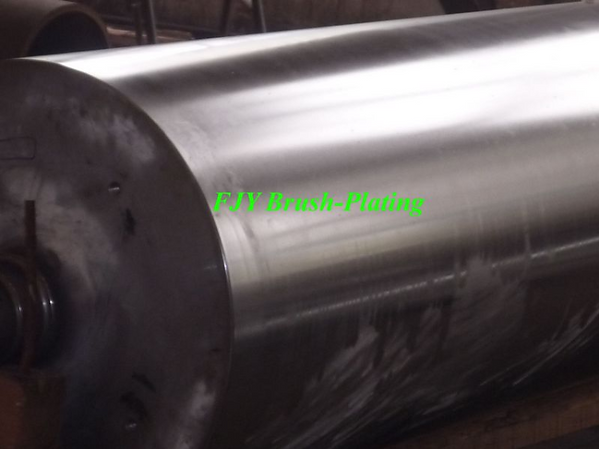

