High corrosion resistant nickel-cadmium anti-corrosion brush plating technology
Introduction to anode anti-corrosion coating on steel surface
There are many ways to prevent or reduce steel corrosion, such as the use of corrosion-resistant materials, coating (plating) layer anti-corrosion technology, corrosion inhibitor anti-corrosion technology, cathodic protection technology, anode protection technology, and perfect structural design. However, in real application and production practice, the most commonly used one is the coating (plating) layer anti-corrosion technology.
The coatings used for the corrosion protection of steel surfaces are mostly anodic coatings (such as zinc, cadmium, and their alloy coatings). They protect against corrosion of the steel matrix by double protection of mechanical protection or sacrificial anode protection (at the expense of themselves to protect the substrate from corrosion). When the coating is flawless, the coating acts as a mechanical protection for the substrate; when the coating is damaged, the anodic coating preferentially dissolves the anode in place of the base metal or slows down the rate at which the base metal is anodic dissolved. Therefore, the chemical stability of the anodic coating in the corrosive medium, the galvanic sequence relationship with the matrix metal, the stability of the surface corrosion product, and the compactness are important factors determining the corrosion resistance.
​
-
Zinc and its alloy coating
​
The galvanized layer is an anodic coating and the passivated galvanized layer provides better corrosion resistance. Due to the low cost of galvanizing, galvanizing of steel surfaces is one of the common methods to prevent steel corrosion.
Since the 1980s, more and more research and application were carried out to introduce other alloying elements (e.g., zinc-nickel, zinc-cobalt, zinc-iron, and zinc-based ternary alloys) into the zinc coating to form zinc-based alloy coatings.
​
2. Cadmium and its alloy coating
​
In equipment that is used in more demanding corrosive environments (such as the maritime environments), or electroplating processes that require extremely high corrosion resistance (such as aircraft landing gear), people tend to use more corrosion-resistant cadmium plating as corrosion protection coating (e.g., aviation high-strength structural parts cadmium-titanium plating) for steel components. However, there are few reports on the research and application of high corrosion resistant cadmium-based alloys.
​
FJY-series high corrosion-resistant cadmium-nickel alloy brush plating technology
In the humid salty environment, the reasons that the cadmium plating layer is highly corrosion-resistant are twofold: 1) cadmium is similar to steel’s galvanic sequence (slightly less than steel) and 2) the corrosion product of cadmium is dense and stable. If a proper amount of nickel is introduced into the cadmium plating to form a cadmium-nickel alloy coating, the corrosion potential is closer to the corrosion potential of the steel. Hence, the mechanical strength of the coating will be significantly increased. In addition, the corrosion life and wear resistance of the coating are further enhanced.
The company has developed a high corrosion-resistant cadmium-nickel alloy brush plating technology that can be used for anti-corrosion of ultra-large steel structures by brush plating. The evaluation on the outdoor environmental corrosion and the anti-corrosion effect of the actual application indicate that using FJY-series cadmium-nickel alloy brush plating technology can significantly improve the service life of equipment (such as offshore oil rigs, wind power equipment).
​
FJY titanium surface brush plating application example (Inexhaustive)
-
Marine wind power equipment surface anti-corrosion brush plating
​
​
​
​
​
​
​
​
​
​
​
​
​
​
​
​
​
​
​
-
Aircraft turbine brush plating FJY anti-corrosion coating
​
​
​
​
​
​
​
​
​
​
​
​
​
​
​
​
​
​
​
​
-
Application of FJY anti-corrosion brush plating on large supersonic wind tunnel
​
​
​
​
​
​
​
​
​
​
​
​
​
​
​
​
​
​
​
​
-
Look of FJY anti-corrosion brush plating layer after 3 years’ exposure on air
​
​
​
​
​
​
​
​
​
​
​
​
​
​
​
​
​
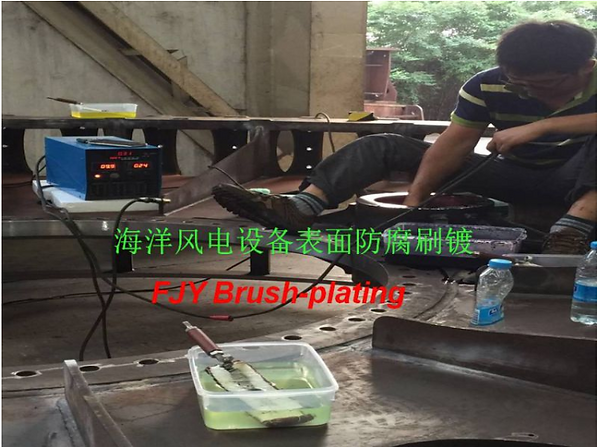


