Reliable repair method of generator rotor shaft wear
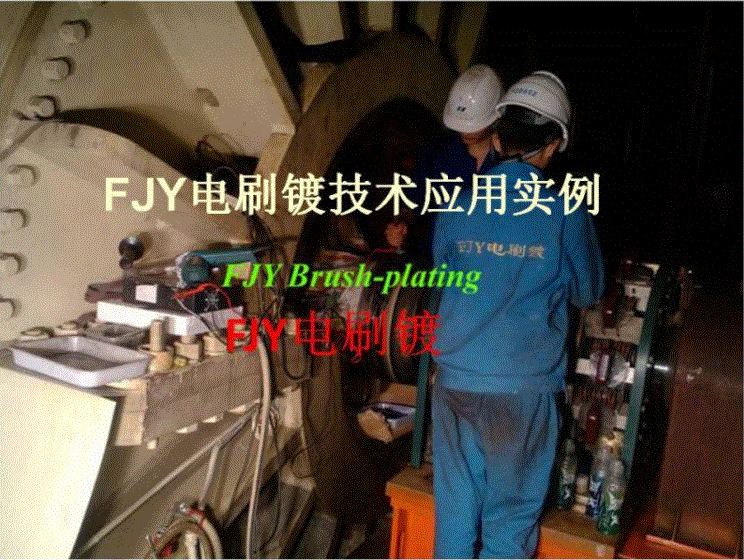
Steam turbine rotor repair
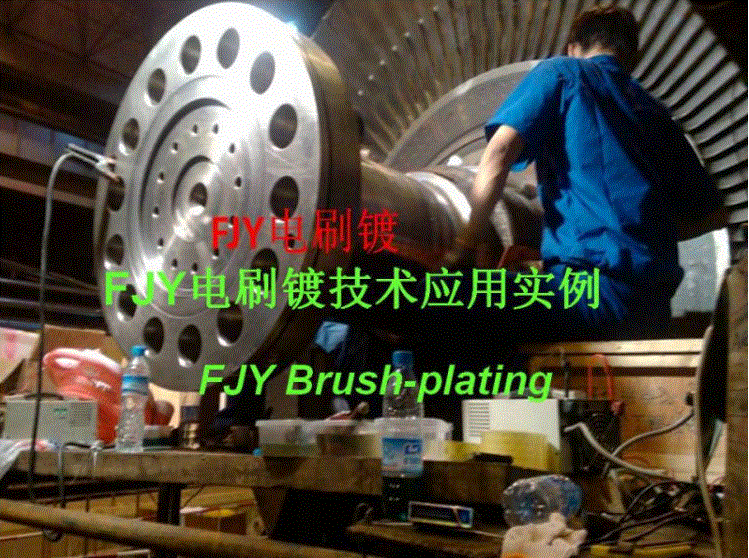
Gas turbine rotor repair
Rotor shaft failure mode
During the operation of the generator set, due to the pollution of the lubricating oil system (such as wear debris, impurities, sealing rubber abrasives), improper oil temperature, oil pressure (cannot form full liquid lubrication), resulting in oil breakage, bushing burning, bearing seizure, and due to the unit Vibration and other reasons cause wear and strain on the rotor journal.
Strains and wear will not only cause changes in the coordination relationship between the components, but also bring hidden dangers to the working status and safety of the generator set. For example, the leakage of generator refrigerant (hydrogen) may detonate the motor (explosive limit of hydrogen). 4~74.2%).
In summary, the wear, out-of-tolerance, and poor electrical connection of power generation equipment will not only affect the normal operation of power plant equipment, but may also bring catastrophic consequences. Therefore, timely repair and maintenance of vulnerable parts of power plant equipment is a guarantee Necessary measures for the normal production of power plants to eliminate potential safety hazards. This article will briefly introduce the special role of FJY series brush plating technology in the maintenance of power plant equipment.
Principles of repairing generator rotor shaft
Wear and strain are the main forms of damage to the generator rotor shaft. Due to the large weight of the generator rotor (weighting tens of tons) and high speed (3000 rpm, or even higher), mechanical vibration and different forms of mechanical wear will inevitably occur during operation. In order to ensure that the repaired rotor will not have dynamic balance problems and reliable maintenance quality, in the process of repairing the rotor shaft, no form of stress (internal stress, mechanical stress) or defects (cracks, pores, Material organization is not uniform, etc.), otherwise there will be bore sweeping or fatigue broken shaft. According to this repair requirement, all heating repair methods (electric welding, surfacing, spray welding, etc.) cannot be used to repair the rotor shaft. Someone has used spraying to repair the worn rotor shaft, but because the sprayed layer and the substrate are mechanically combined, the rotor vibration will cause the coating to drop slag and again produce abrasive wear. In principle, the laser cladding method (laser with low power and low heat generation) has the characteristics of cold welding, but the equipment is expensive and not suitable for on-site maintenance. At present, only cold welding technology (patch cold welding method, gas shielded fuse cold welding method) can barely be used for rotor repair. Compared with FJY electric brush plating repair technology, the use of FJY electric brush plating method to repair the rotor has better comprehensive performance.
A new method of repairing rotor shaft - FJY brush plating technology
The generator rotor shaft is made of high alloy steel (such as 35 Cr Mo, 26 Cr2Ni4MoV, etc.). The brush plating process can be formulated in accordance with the brush plating method of alloy steel substrate in the "FJY Series Brush Plating Technology User Guide". For the repair of the journal strain, the basic process is: mechanical shaping (widen the groove, the bottom of the groove is bright, and the transition is smooth), electric cleaning, water washing, 2 activation, water washing, 3 activation, water washing, alloy steel activation , Alloy steel bottom nickel, water washing, ion cold welding of nickel-based alloy (or hard copper alloy) to fill the grooves, polish out, and cover the surface layer.
If the repair is an oil pressure-sealed bush, after the journal is repaired, bushes should be matched or scraped according to the journal size to ensure proper oil clearance so that liquid lubrication can be formed between the shaft and the bushes during normal operation. If the bearing position of the rotor shaft is to be repaired, the entire mating surface should be restored to the design size and accuracy to facilitate replacement of the new bearing.
Generally, the commonly used brush plating process seldom takes into account the nature of the substrate. Usually, a set of processes is used for brush plating repair of parts with multiple materials, which is not targeted and the use effect is unstable (sometimes good, sometimes bad). With the rapid development of modern brush plating technology, FJY series brush plating technology has developed a complete set of quick repair methods specifically for high-alloy steel generator shafts. The plating layer and the substrate are combined with a metal bond. There will be no peeling of the coating, and the repair quality is stable and reliable. For example, a 350MW generator rotor shaft repaired by FJY brush plating technology in a thermal power plant in Xinjiang in 2007 is still in normal use. FJY brush plating technology has the characteristics of fast and super thick, which provides convenience for the general use of this technology. In addition, the brush plating method can perform non-disintegration repair of the rotor in the power plant, which is simple and easy to implement.